Signs You Need Professional Packaging Machine Repair Right Away
Signs You Need Professional Packaging Machine Repair Right Away
Blog Article
Quick and Reliable Product Packaging Device Repair Work Provider to Lessen Downtime
In the affordable landscape of production, the performance of packaging procedures rests on the integrity of equipment. Quick and trusted fixing services are vital in minimizing downtime, which can cause significant operational obstacles and financial losses. Recognizing the value of timely interventions and the function of expert professionals can transform how organizations come close to repair and maintenance. Nevertheless, navigating the myriad options available for repair service services can be difficult. What aspects should businesses think about to guarantee they are making the ideal selection for their operational requirements?
Importance of Timely Repair Works
Timely repair services of packaging makers are vital for keeping functional performance and lessening downtime. In the hectic setting of manufacturing and product packaging, even minor malfunctions can lead to significant hold-ups and performance losses. Addressing problems quickly makes sure that equipments run at their optimum capability, thus protecting the flow of operations.
Moreover, regular and prompt maintenance can avoid the acceleration of minor problems right into significant break downs, which frequently incur higher fixing expenses and longer downtimes. A proactive approach to equipment repair service not just maintains the integrity of the tools however also enhances the general dependability of the assembly line.
In addition, timely repairs contribute to the long life of packaging equipment. Makers that are serviced without delay are less most likely to struggle with too much damage, allowing services to maximize their investments. This is particularly vital in markets where high-speed packaging is necessary, as the requirement for regular performance is extremely important.
Advantages of Reliable Company
Trustworthy service suppliers play a pivotal role in making sure the smooth operation of product packaging equipments. Their knowledge not only boosts the efficiency of repair work however likewise contributes substantially to the long life of tools.
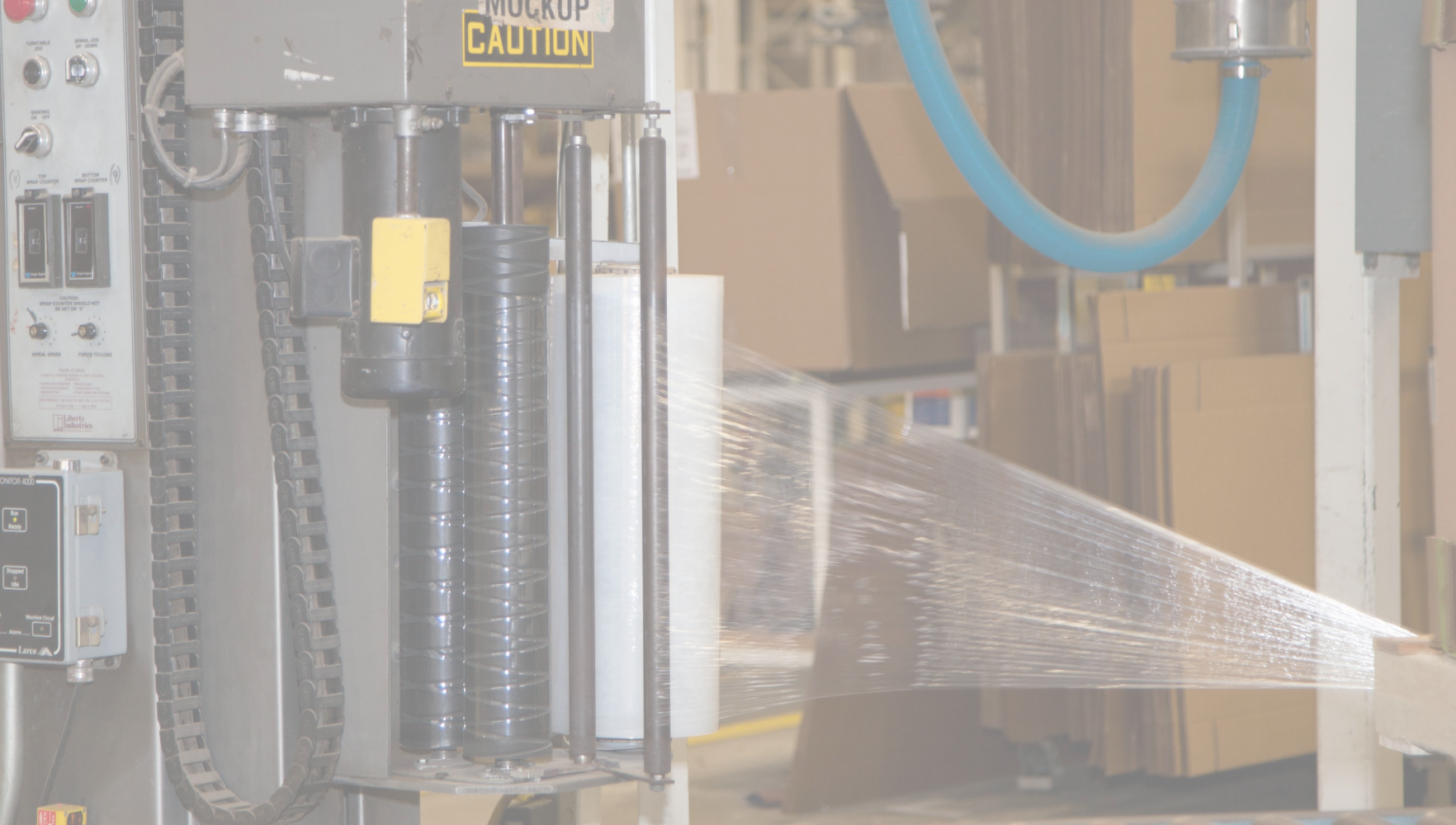
Additionally, a trustworthy provider uses detailed support, including training and assistance for staff on device operation and upkeep best practices. This not just encourages staff members however likewise grows a society of security and efficiency within the organization. Overall, the advantages of involving reputable solution providers extend beyond prompt fixings, favorably impacting the entire operational operations of product packaging processes.
Common Product Packaging Maker Issues
In the realm of packaging operations, numerous problems can compromise the efficiency and capability of machines. One widespread issue is mechanical failure, often originating from deterioration or inadequate maintenance. Components such as motors, equipments, and belts might fail, bring about break downs that stop manufacturing. Another typical issue is imbalance, which can create jams and unequal product packaging, affecting product high quality and throughput.
Electrical issues can additionally disrupt product packaging find out here procedures. Defective circuitry or malfunctioning sensors may lead to irregular machine behavior, creating delays and increased operational prices. Additionally, software application glitches can prevent the machine's shows, leading to functional inadequacies.
Inconsistent product flow is one more critical problem. This can emerge from variations in product dimension, form, or weight, which may affect the device's capability to take care of things accurately. Finally, insufficient training of operators can intensify these issues, as untrained workers may not acknowledge early signs of malfunction or may misuse the equipment.
Dealing with these typical packaging equipment issues quickly is necessary site here to keeping performance and making certain a smooth procedure. Routine evaluations and proactive maintenance can significantly minimize these problems, promoting a trustworthy product packaging atmosphere.
Tips for Reducing Downtime
To minimize downtime in product packaging operations, executing a proactive maintenance approach is vital. Consistently arranged maintenance checks can recognize prospective issues prior to they intensify, ensuring equipments operate efficiently. Developing a routine that consists of lubrication, calibration, and assessment of crucial parts can substantially decrease the regularity of unexpected failures.
Educating personnel to run machinery appropriately and identify very early warning signs of breakdown can also play a crucial role. Equipping operators with the understanding to perform fundamental troubleshooting can prevent minor issues from triggering significant hold-ups. Furthermore, keeping an efficient supply of crucial spare parts can accelerate fixings, as waiting on components can result in prolonged downtime.
In addition, recording machine performance and maintenance tasks try this website can aid recognize patterns and recurring problems, enabling for targeted treatments. Including innovative monitoring technologies can offer real-time information, making it possible for predictive upkeep and minimizing the danger of abrupt failures.
Finally, cultivating open communication in between operators and upkeep groups makes certain that any irregularities are quickly reported and attended to. By taking these aggressive procedures, organizations can boost functional effectiveness and dramatically lower downtime in product packaging procedures.
Selecting the Right Repair Work Service
Choosing the appropriate fixing service for product packaging makers is a vital decision that can substantially affect operational efficiency. Begin by evaluating the provider's experience with your details kind of packaging devices.
Following, think about the provider's track record. Looking for comments from other organizations within your market can give insights right into reliability and high quality. Qualifications and collaborations with recognized tools producers can additionally indicate a commitment to quality.
Additionally, examine their reaction time and accessibility. A service company that can offer timely assistance minimizes downtime and maintains manufacturing flow consistent. It's additionally essential to ask about warranty and solution warranties, which can reflect the confidence the copyright has in their work.
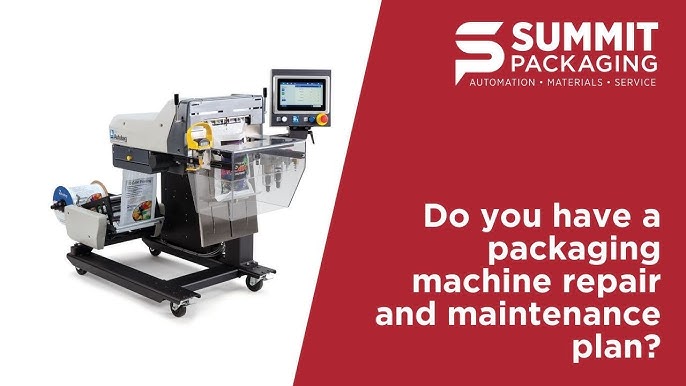
Final Thought
In final thought, the value of quick and trustworthy product packaging equipment repair solutions can not be overemphasized, as they play an important duty in minimizing downtime and guaranteeing operational effectiveness. Applying proactive maintenance practices and spending in team training more enhances the longevity of product packaging equipment.
Prompt repair work of product packaging equipments are crucial for maintaining operational efficiency and reducing downtime.Furthermore, timely repair services add to the long life of product packaging equipment. Generally, the advantages of involving trustworthy solution suppliers expand past prompt fixings, favorably influencing the whole functional process of packaging processes.

Report this page